All of the steel parts came back from being cut at the water jett shop and we had our parts check and first welding consult with the folks at Stephen’s Machine Shop in Kokomo yesterday. That is Ken ( on the right) and Steve ( on the left)- who are working with us to get the base prepped and welded. We decided to work with folks who weld Stainless all day every day to ensure that the base is completely secure. We also believe that art is collaborative and like to work with local professionals who can help us out.

Parts check means that we go through stacks of parts, checking cut, sizing and fit. We also needed to talk through where the base welds need to be placed and how to avoid warpage to the stainless as much as possible.
The big gears came back stunningly gorgeous, we could not be more pleased.
This is the base gear – you can see the flat edge where it gets welded down to the base plate.
The long bats will get filled with Kokomo Opalescent Glass, and the rounds will remain open.
Parts checking is not just all marveling at the beauty of the pieces and playing with forklifts.
It is also time for careful measurement checks – here you can see Ken with his calipers, checking hole sizes; lining up pieces to make sure that the alignments came out correctly, and lots of talking and planning. Once the pieces are welded, it is too late to find out about misunderstandings or mis-communications. Like any other project, the up front planning is critical to success. We were very pleased with the amount of time and thought Ken and Steve contributed to making sure that the piece gets done correctly.

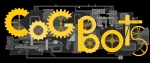
They will start the actual welding within a week, and we will get the chance to video tape for you, so watch for updates.